

Left: Finite Element tetrahedral mesh, SOLIDWORKS Simulation.

This enables a technology called solution-adaptive meshing, where the solver can refine and improve the mesh during the calculation without having to start from scratch, greatly increasing the accuracy of your results in a short amount of time.
#SOLIDWORKS FLOW SIMULATION HELP UPDATE#
With this methodology, the size and shape of the 3D model and fluid space remains constant, but the mesh itself (in this case a Cartesian grid) can change and update during the simulation. Unlike the more common approach of Finite Element Analysis, where a model is broken up into a fixed number of elements (like tetrahedrons or triangles), SOLIDWORKS Flow Simulation uses a technique called the Finite Volume approach. One major example of this has to do with meshing, which influences both the solve time and the accuracy of your results. While speed and a shallow learning curve are key benefits of using SOLIDWORKS Flow Simulation, there are also some powerful computation abilities that can give users an advantage in solution accuracy compared with other products on the market. SOLIDWORKS Flow Simulation Meshing Basics SOLIDWORKS Flow Simulation is one example of this, allowing any design engineer to test fluid behavior and heat transfer directly on their existing 3D models.
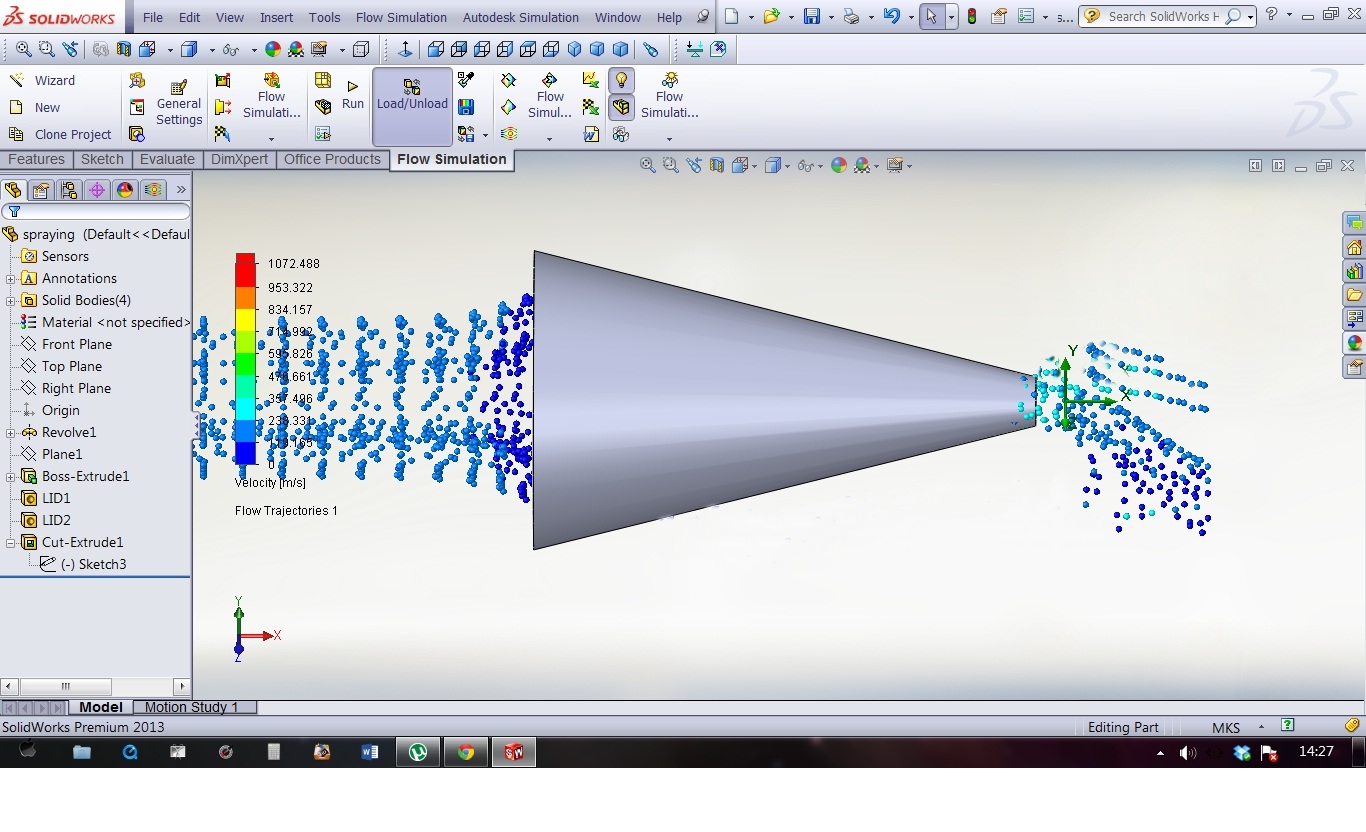
If you’re a user of SOLIDWORKS, you’re probably aware that Dassault Systèmes also offers a family of products that go beyond just CAD without having to leave the familiar SOLIDWORKS design environment.
